Hassan Touil’s journey to build a better life has brought him halfway around the world. He grew up in Morocco, graduating from high school there and studying law in college before suddenly getting the chance of a lifetime – he and his wife, Bouchra Abouzayd, were selected in the immigration lottery to move to the United States.
Touil, whose first language is Arabic and second language is French, had studied Italian in college but didn’t speak a word of English. Unwilling to let that barrier stop them from pursuing their dreams, he and Abouzayd jumped at the chance to start a new life and in 2010 settled in central Connecticut, where Touil then 33, enrolled in English as a Second Language (ESL) classes at Meriden Adult Education.
The following year, Touil landed a job at Radio Frequency Systems in Meriden, where he spent six years, working in assembly, WiFi quality control, and machine repair. But in 2017, the work performed by his department was outsourced to China, and he and his coworkers were laid off.
Undeterred, Touil – who now was the father of two young children under the age of 5 – returned to Meriden Adult Education with assistance from the Department of Labor to improve his English and get ready to return to employment. Hassan’s ESL teachers encouraged him to enroll in a program called Transitions, a collaboration between Middlesex Community College and Meriden Adult Education designed to help motivated students prepare for credit or non-credit college studies. While fortifying his literacy and numeracy skills, Hassan was given information about an innovative new jobs training program called “Skill Up for Manufacturing,” and applied.
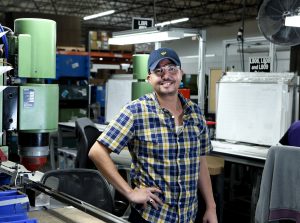
For Touil, the free 5-week course represented yet another incredible opportunity. Students who were accepted into the program would be given the exact type of training requested by local manufacturers, along with direct introductions to those firms. Based on experience with the program, organizers explained that this would almost certainly lead to a full-time job within a short time frame – all without incurring any student debt.
The manufacturing pipeline initiative or MPI, initially developed by the Eastern Connecticut Workforce Investment Board, is now also offered by its sister agency, New Haven-based Workforce Alliance. The goal of the program, dubbed “Skill Up” in New Haven and Middlesex Counties, is to help local manufacturers find skilled workers, and to provide lucrative career opportunities for students willing to undergo the customized training they need to be successful.
For Touil, this new chance to improve his life came with certain conditions. It required him to earn an American GED credential (his Moroccan high school diploma and college studies didn’t count), pass an English test (he scored 74) and become even more proficient in math. He started the program this past summer and threw himself into his studies.
It wasn’t easy. “You have to work a lot,” he says. “You go in at 8 a.m. and you finish at 4 p.m, every single day, like you’re working [full time] or training for a job.” By day, the students take classes in everything from shop mathematics to metal cutting. At night, says Touil, “you have to go home to work online, [studying subjects] like intro assembly, intro to fasteners, torque, basic tolerance and trade inspections, because you have tests online every second day.”
Before graduating from the program with a certificate in NIMS manufacturing (standards set by the National Institute for Metalworking Skills) in August, he and his classmates were given the chance to meet with several manufacturing companies in a job-fair type of setting at the college. Touil made a beeline for the table of Roto Frank of America, a Chester-based manufacturer of window and door hardware, and spoke with HR manager Sylviana Lopez.
“I asked her for [a job at] the company because it is not so far from my home. I was looking for a job that was 15 to 20 minutes from my home to work,” he recalls. The interview went well and within a month of graduating, he was hired.
Lopez, who offered all of the students at the meet-and-greet a tour of her company and an opportunity to apply for a job, says she recalls meeting Touil for the first time. “He was one of the first ones who came to my table and he said, ‘I’m looking for a job – anything that’s open. This is my resume and I would like to go for a tour.’ I remember giving him my card. I said, ‘Call me or send me an email and then we will get you in and at least show you around, until a job comes up.’ ”
She says Touil did everything right when it came to boosting his employment prospects.
“Of all the participants, he was the first one I received an email from, saying thank you,” she recalls. Although there weren’t any openings at Roto Frank by the time the “Skill Up” program ended, he asked for, and received, a tour and sent a thank you note afterwards. “He kept calling and saying, ‘Hey, I just want to know if there’s [a position] yet. He was very nice, very eager and very interested. I talked to the plant manager and said, ‘We need someone like that.’ And the manager said, ‘Yeah, let’s bring him over.’ And Hassan has been great.”
In fact, Touil was recently selected from among the company’s newest hires to receive forklift training. “We said, ‘Let’s give it to Hassan; he seems very eager to learn and he has very good attendance. He’s a very, very good person,” says Lopez. “He was thrilled when I told him, ‘They want you in this position now because they think that you have potential and that you’ll learn really fast.’ In the area where he works, they were telling me that he was really good from the day he started.”
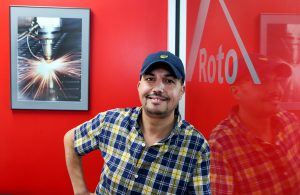
Too many jobs, not enough workers
Connecticut has long faced a shortage of qualified workers to fill positions in the state’s manufacturing industry. Four years ago, having realized that this situation would not improve without a targeted effort to address it, the Eastern Connecticut Workforce Investment Board (EWIB) applied for and received a three-year, $6 million U.S. Department of Labor grant to identify unemployed and underemployed job candidates, and offer them specialized training for positions with manufacturers in the region. In return, the EWIB, led by president John Beauregard, promised to fill 400 jobs.
The board worked closely with educational institutions and area manufacturing firms to determine the exact type of training needed and then offer it at no cost to students. The results have exceeded all expectations. Since the pipeline program began, nearly 2,000 participants have been trained at local schools and colleges and placed in jobs. Roughly 200 manufacturers, both large and small, have been hiring through the program.
“That was the intent here – to make sure that not only large employers but smaller and medium employers had a place to turn to for the development of tomorrow’s manufacturing workforce,” Beauregard says.
Since the program started, eastern Connecticut has seen ongoing economic growth, much of it attributed to an expansion in advanced manufacturing and eastern Connecticut’s “unique ability to find the workforce talent for that sector,” says economist Don Klepper-Smith. “The MPI program has provided a clear and dramatic boost to the economy.” He says in addition to putting more money in people’s pockets, the jobs pipeline has prompted more people to buy homes.
Meanwhile, applicants are streaming into the program, lured by the prospect of a lucrative and interesting career. Because the training curriculum and standards are designed and set by employers, students’ chances of being hired once they graduate are high, even though almost 80% have had no previous manufacturing experience.
With millions in additional funding provided by the state and private sources, the original timeline for the program has been extended. Over the next few years, Beauregard says, Electric Boat plans to spend more than $800 million on construction projects related to the development of its new Columbia class submarine. “So, obviously, there will be a great need for construction workers.”
Hoping to see this successful model used elsewhere, the board shared its approach with its New Haven counterpart, which launched its first program this past February. New classes will begin in Middletown, New Haven, and Groton in early 2020. (See information box for more details.)
William P. Villano, president and CEO of Workforce Alliance for the south central region of Connecticut, says the “Skill Up” program, offering entry-level training, crams a lot of material into five weeks, noting, “this allows us to train a lot of people very quickly.” He says figures released by the Connecticut Business & Industry Association (CBIA), show that there are 8,000 to 10,000 manufacturing positions currently open in Connecticut, and 85% of employers are having a tough time finding the qualified workers they desperately need – or retaining the ones they have. While the sector is slowing down a bit due to concerns about international trade and tariffs, manufacturing led the state in jobs growth in 2018 and 2019.
Meanwhile, Eric Brown, CBIA’s vice president of manufacturing policy and outreach, has been working with his team over the past 18 months to create new initiatives aimed at shifting the already vigorous manufacturing sector into an even higher gear. For instance, a new Connecticut Manufacturers’ Collaborative has been formed to help manufacturers work together to drive positive change.
Brown says the state’s companies are in “a time of transition. It’s a challenge for manufacturers to gain awareness of technologies that might be helpful for them, and to keep up – not just in the state but globally – with the technology associated with manufacturing advancements.”
And he warned that the pace of change isn’t going to change any time soon, except to speed up. “Manufacturers tell us that over the next five years, the advancements are going to be rather dramatic. The industry is going to need higher skilled workers to not only use these technologies but to create them, to build them, to service them. It’s going to be a continual upward trend.”
Although the eastern Connecticut pipeline program has been catering largely to Electric Boat and its supply chain, New Haven and Middlesex counties have “a little more diversity in terms of the types of manufacturing that goes on,” says Villano – producing everything from medical devices and aerospace components to specialty lighting and labels. He says the region “has a lot of little small shops but a significant number of them,” as well as larger players like Pratt & Whitney, Sikorsky, Sargent ASSA ABLOY, and Ulbrich.
Based on the latest data, he says, Rosa DeLauro’s Congressional district represents the second largest percentage of manufacturing jobs in the state (24%), second only to the Hartford region at 28%.
The number of available manufacturing jobs available in Connecticut will only continue to grow as Baby Boomers in the sector retire, a phenomenon that Villano calls “the Silver Tsunami.” The state’s half-dozen manufacturing associations have been scrambling to find replacement workers, with older workers who delayed retirement when the Great Recession hit in 2008 now finally leaving their careers.
That spells fresh opportunity for a newer generation, he says.
Applicants for the “Skill Up” program must be at least 18 years old, reside in Connecticut, have a high school diploma or GED, and be eligible to work in the U.S. After applying online at www.workforcealliance.biz/skillup, applicants are contacted, undergo an orientation, and take a two- to three-hour test in subjects like shop math, spatial reasoning and measurement.
Roughly 60% of the people who apply to “Skill Up” are in the 25 to 45 age range, with just 15% in 18 to 24 age range, although both young and middle-aged applicants are welcome.
“It’s surprising to see the number of people who are over 45 who are looking to get into this program, and there’s an increasing number of women,” Villano says. If applicants struggle with the math component, they can take a two-week boot camp “that hopefully brings people up to the speed that we need, and gives them another shot at the test.”
The core program, he says, is “very intensive. It covers blueprint reading, different types of manufacturing processes and safety.” Employees complete their training on the job once they are hired. He points out that this program can also benefit those people looking to use prior manufacturing experience and education in a new way.
Partnering with Gateway, Middlesex and now Three Rivers community colleges, the “Skill Up” program is open to anyone in Connecticut. When the next round of state funding comes through, the program will begin offering welding and design, which are already part of the curriculum in eastern Connecticut.
Plans are also in the works to branch out beyond manufacturing to healthcare, hospitality, transportation and logistics, which will provide even more opportunities for Connecticut residents to train – or retrain – for a well-paying career job.
“We’re showing an average starting salary of over $16.30 and many manufacturers have 90-day or 6-month reviews and will add to that [rate]. One of our graduates with past experience landed a $70-an-hour job as a plant manager.”
There are significant benefits for companies who hire from the program, too. Villano points to one company in Old Saybrook that had had no steady workforce, instead relying on temporary workers. “The president of the company was involved in the eastern program and has saved $100,000 per year on temp labor costs. A successful grad brings a lot more to the table than someone hired off the street.”
Villano and his team are working hard to spread the word about the program – linking the application portal to social media, working with education partners to promote it, doing media relations, and talking about it at graduations. News is also spreading by word of mouth. In addition, Workforce Alliance operates several of the state’s American Job Centers (New Haven, Middletown, Hamden, Meriden), where unemployed or underemployed people come in for help to find a good job but may not know just what they’re looking for.
He feels that in today’s environment, where there is a lot of discussion about the value of an expensive college education and the burdens associated with significant student debt, people need to recognize – including students and their parents – that manufacturing is a good, steady career. “If Electric Boat never got another new contract, they would still have enough work until 2037. Pratt & Whitney has a backlog of engine work. Sikorsky has a backlog of heavy lift helicopter orders. There’s not a lot of other industries where you can go and have a job for the next 20 years,” he says.
He adds that the industry has evolved to an amazing extent. The idea that manufacturing is “dirty, dark and dangerous” couldn’t be further from the truth. “Manufacturing has become very technical,” says Villano. “You can eat off the floor in most places. The biggest issue is making people understand that manufacturing is alive and well in Connecticut, and convincing parents, students and school advisors that this is a great career.”
If there’s one person who needs no convincing, it’s Hassan Touil, who is happily ensconced in his job at Roto Frank of America. Touil, now 42, feels secure in his new position and loves the upbeat team atmosphere. “I’m very happy here,” he says. “Everybody helps each other. You can ask anything that you don’t know, and they will help you. They’re nice people.”
The feeling is mutual, according to Lopez: “We are very happy and very pleased with Hassan.”
Photographed by Stan Godlewski
More Stories
Over 50, Underestimated: The Grandfluencers Redefining Age on Social Media
Building Resilient Businesses: Strategies for Success
Summer Means Convertibles